Molybdenum Oxide in Thin Film Deposition: Benefits, Applications, and Comparisons
views, Updated: 2024-12-27
Introduction
In the world of modern electronics, optoelectronics, and energy applications,
thin film deposition plays a fundamental role in creating materials that are both functional and versatile. One of the key materials that have gained significant attention in recent years is
molybdenum oxide (MoO₃). This compound is a highly stable inorganic material that, when deposited as a thin film, exhibits a unique combination of electrical, optical, and thermal properties that make it highly valuable in a wide range of advanced technological applications.
The process of
thin film deposition refers to the application of a very thin layer of material onto a substrate to form a functional coating, often with properties different from those of the bulk material. Molybdenum oxide, in particular, has emerged as a critical player in this field, contributing significantly to the performance and efficiency of devices such as solar cells, sensors, transistors, and optical coatings.
Molybdenum Oxide: A Powerful Material for Thin Film Deposition
Molybdenum oxide is favored in thin film deposition due to its chemical stability, high melting point, and versatile electrical properties. When deposited as a thin film, MoO₃ can perform as a semiconductor or insulator, making it suitable for a variety of applications. Its role in thin film technology is multifaceted and can vary depending on the specific deposition method and the desired properties of the thin film.
A key feature of MoO₃ is its ability to form films with excellent optical properties, high thermal stability, and a good adhesion profile. These properties make MoO₃ an essential component in the fabrication of high-performance devices, such as solar cells, sensors, and various types of optoelectronic devices.
Why Molybdenum Oxide?
Molybdenum oxide has several properties that make it a preferred choice for thin film deposition:
1. Electrical Properties: MoO₃ has a high work function and can be tailored to show either insulating or semiconducting properties, which makes it suitable for a wide range of electronic and optoelectronic applications.
2. Optical Transparency: MoO₃ thin films are highly transparent in the visible light spectrum, making them ideal for use in transparent conductive films used in displays, solar cells, and touchscreens.
3. Thermal and Chemical Stability: Molybdenum oxide remains stable at high temperatures and in harsh environmental conditions, which ensures that devices using MoO₃ thin films maintain their performance over extended periods.
4. Versatility in Deposition: MoO₃ can be deposited using several methods, including sputtering, chemical vapor deposition (CVD), and pulsed laser deposition (PLD). This flexibility allows for its integration into a variety of manufacturing processes. As a leading supplier of
Molybdenum oxide sputtering targets, we provide flexible solutions that integrate seamlessly into a wide range of manufacturing processes.
5. Sustainability: Molybdenum is an abundant element, making MoO₃ a more sustainable option compared to other precious metal oxides like silver oxide or gold oxide, which are more expensive and harder to source in large quantities.
These attributes have helped position molybdenum oxide as a critical material for advancing technologies in sectors like green energy, wearable electronics, and environmental sensing.
Applications of Molybdenum Oxide Films
Molybdenum oxide (MoO₃) films are becoming essential in many high-tech industries due to their unique electrical, optical, and thermal properties. These thin films are used in a variety of applications, from solar energy and displays to sensors and coatings. Their ability to be precisely applied makes them a key material in advanced technologies. Below, we explore how MoO₃ films are used across different fields to improve device performance, efficiency, and functionality.
1. Solar Cells
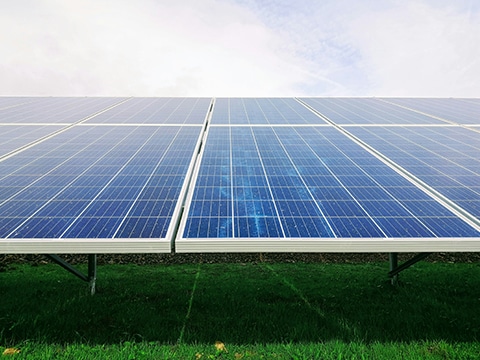
Molybdenum oxide films play an important role in solar energy, especially in thin-film solar cells. They are commonly used as a hole transport layer (HTL) or buffer layer in organic and perovskite solar cells. MoO₃ helps improve the collection of electrical charges, enhances the stability of the solar cells, and reduces energy losses.
In organic solar cells, MoO₃ films improve the efficiency of charge transfer between the semiconductor and electrode, boosting overall solar cell performance. MoO₃’s transparency and conductivity also make it ideal for use in transparent electrodes, which are critical for efficient and cost-effective solar panels.
2. Organic Light Emitting Diodes (OLEDs)
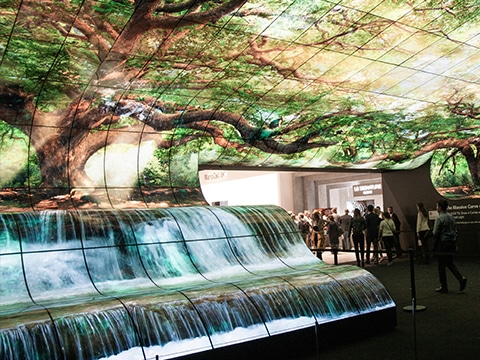
MoO₃ films are widely used in OLEDs, which are found in displays and lighting. In OLEDs, MoO₃ is typically used as a hole injection layer (HIL), helping charge to move smoothly into the organic material. This increases the efficiency of the device and reduces energy loss.
MoO₃’s high work function allows for better hole injection, which results in brighter and more energy-efficient OLEDs. Its transparency is also crucial, particularly for transparent or flexible displays, making MoO₃ an essential material for next-generation OLED technology.
3. Gas Sensors
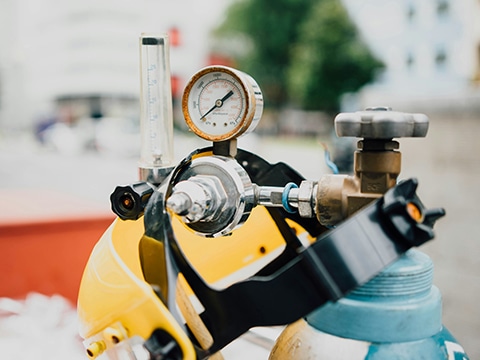
MoO₃ films are used in gas sensors to detect gases like ammonia (NH₃), carbon dioxide (CO₂), nitrogen dioxide (NO₂), and hydrogen (H₂). MoO₃’s high surface area and chemical reactivity allow it to detect small amounts of gases in the environment.
When MoO₃ interacts with gases, its electrical conductivity changes, which is measured to identify the presence of specific gases. These sensors are used in applications like air quality monitoring, industrial safety, and environmental control. MoO₃ films can also perform well in harsh conditions, such as high temperatures or chemically aggressive environments, making them reliable for smart sensors used in automotive and industrial settings.
4. Thin Film Transistors (TFTs)
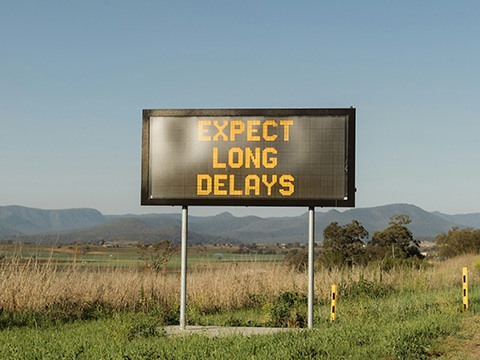
MoO₃ films are a key component in Thin Film Transistors (TFTs), which are used in electronic displays like LCDs and OLEDs. MoO₃ is used in TFTs to improve the performance of the gate electrode or source-drain contacts, helping switch pixels on and off for high-quality images.
MoO₃’s high work function helps charge carriers move efficiently into the active layer of the transistor, improving its speed and mobility. This results in better performance for displays. MoO₃’s stability also ensures that TFTs maintain their performance over time, extending the lifespan of the devices.
5. Catalysis and Energy Storage
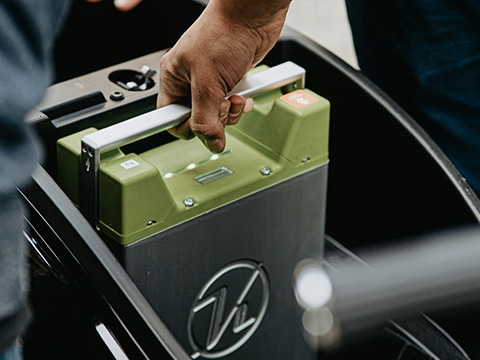
MoO₃ films are used in catalysis and energy storage. As a catalyst, MoO₃ speeds up chemical reactions, such as the oxidation of organic compounds or hydrogen production, making these processes more efficient.
In energy storage, MoO₃ has been tested for use in supercapacitors and batteries. Its ability to undergo reversible chemical reactions makes it ideal for energy storage applications, helping to increase the energy density and efficiency of devices like supercapacitors.
6. Wearable Electronics
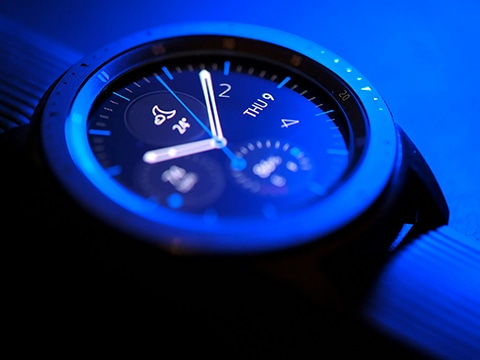
MoO₃ films are ideal for wearable electronics due to their flexibility, transparency, and conductivity. These properties make them perfect for use in devices like smartwatches, fitness trackers, and other wearable health monitors.
The flexibility of MoO₃ allows it to withstand bending and stretching without losing performance, which is essential in wearable applications. Its high thermal stability ensures that the devices can function in varying environmental conditions, making MoO₃ films a reliable choice for wearable technology.
Molybdenum oxide films are incredibly versatile and used in a wide range of applications, from solar cells and OLEDs to gas sensors and wearable electronics. Their unique combination of electrical, optical, and chemical properties makes them indispensable for the development of advanced technologies. As research in this field continues, the potential applications of MoO₃ films are expanding, promising even more breakthroughs in electronics, energy solutions, and smart technologies.
Molybdenum Oxide vs Other Materials in Thin Films
When it comes to thin film deposition, choosing the right material is crucial for the success of your project. Molybdenum oxide (MoO₃) stands out as a versatile material, but it's not the only one. There are other materials like indium tin oxide (ITO), tungsten oxide (WO₃), and vanadium oxide (VO₂) that are commonly used in thin films too. Each has its own strengths and weaknesses, depending on the specific application.
In this section, we’ll compare MoO₃ with some of the other popular materials in thin film technology. We’ll break down how MoO₃ measures up in terms of cost, performance, optical properties, and durability. Let’s dive into how MoO₃ stacks up against these other materials, and why it might be the best choice for your next project.
1. MoO₃ vs. Indium Tin Oxide (ITO)
Indium Tin Oxide (ITO) target is one of the most widely used materials for transparent conductive films (TCFs), especially in touchscreens and displays. ITO offers great optical transparency and high electrical conductivity, which makes it the go-to material for many electronic devices. However, it’s not without its downsides.
Advantages of MoO₃ Over ITO
-
Cost: ITO is made from indium, a rare and expensive metal, which drives up the cost of using ITO in large-scale applications like solar panels and displays. Molybdenum, on the other hand, is more abundant and much cheaper, making MoO₃ a more cost-effective option for many industries.
-
Sustainability: Because indium is scarce, it raises concerns about the long-term sustainability of ITO. Molybdenum, however, is more abundant and easier to source, making MoO₃ a better option for eco-friendly applications.
-
Thermal Stability: MoO₃ is more stable at high temperatures compared to ITO. In high-temperature environments like solar cells or electronic devices, MoO₃ holds up better over time, while ITO may degrade.
Drawbacks of MoO₃ Compared to ITO
-
Electrical Conductivity: While MoO₃ offers decent conductivity, ITO typically outperforms MoO₃ when it comes to pure electrical conductivity. This makes ITO a better option for applications where super high conductivity is needed, like in some high-performance displays.
2. MoO₃ vs. Tungsten Oxide (WO₃)
Tungsten oxide (WO₃) target is another material used in thin films, especially in smart windows and electrochromic devices, where it’s valued for its ability to change color in response to an electric charge. But how does it compare to MoO₃?
Advantages of MoO₃ Over WO₃
-
Electrical Properties: MoO₃ films are more flexible when it comes to electrical properties. They can be tailored to work as insulators or conductors depending on the needs of the application. WO₃, on the other hand, is typically more insulating in nature, which limits its use in certain electronic applications.
-
Optical Transparency: MoO₃ offers higher optical transparency than WO₃, especially in the visible light spectrum. This makes MoO₃ more suitable for transparent conductive films used in devices like solar cells and touchscreens, where clear visibility is important.
Drawbacks of MoO₃ Compared to WO₃
-
Electrochromic Applications: WO₃ is better known for its electrochromic properties, meaning it can change color when voltage is applied. This makes it ideal for smart windows and other color-changing devices. MoO₃, while useful in many applications, doesn’t have the same electrochromic abilities as WO₃.
3. MoO₃ vs. Vanadium Oxide (VO₂)
Vanadium oxide (VO₂) target is famous for its temperature-sensitive properties. It undergoes a metal-insulator transition near 68°C, making it useful for temperature sensing and smart windows that automatically adjust to changes in temperature. Let’s see how MoO₃ compares.
Advantages of MoO₃ Over VO₂
-
Electrical Stability: MoO₃ offers more consistent electrical behavior than VO₂. VO₂ has a unique property where it changes from an insulator to a metal when the temperature rises past a certain point. This transition can be useful for specific applications, but it can also be unpredictable. MoO₃, on the other hand, has more stable electrical properties across a range of temperatures, which makes it more reliable for many applications.
-
Optical Transparency: MoO₃ generally offers better optical transparency than VO₂, which makes it a better choice for transparent films in displays and solar cells where clear visibility is key.
Drawbacks of MoO₃ Compared to VO₂
-
Temperature Sensitivity: VO₂’s ability to change from a metal to an insulator with temperature makes it unique and very useful for applications in smart windows and thermal sensors. MoO₃ doesn’t exhibit this kind of dramatic temperature-dependent behavior, so it’s less suited for applications that rely on temperature-switching properties.
4. MoO₃ vs. Tin Oxide (SnO₂)
Tin oxide (SnO₂) target is another material often used in transparent conductive films and gas sensors. It’s known for its good conductivity and chemical stability.
Advantages of MoO₃ Over SnO₂
-
Higher Transparency: MoO₃ offers better optical transparency than SnO₂, especially in the visible light spectrum. This makes MoO₃ a better choice for transparent conductive films used in displays and solar cells, where clarity is crucial.
-
Electrical Tunability: MoO₃ is more flexible in terms of adjusting its electrical properties to fit the needs of different applications. SnO₂ is usually more conductive, which can limit its use in devices that require a range of electrical properties.
Drawbacks of MoO₃ Compared to SnO₂
-
Environmental Stability: Tin oxide has better chemical stability and is less likely to degrade when exposed to moisture or chemicals compared to MoO₃. This makes SnO₂ a better choice for applications in harsh environments, such as gas sensors in industrial settings.
Conclusion
Molybdenum oxide (MoO₃) target is becoming a top choice for thin film applications thanks to its amazing properties. Whether used in solar cells, OLED displays, sensors, or transparent films, MoO₃ offers a unique mix of benefits that make it an ideal material for many industries.
One of the best things about MoO₃ is how versatile it is. It can be used in different environments because it’s heat-resistant, chemically stable, and can be adjusted to have the right electrical and optical properties for each application. This makes MoO₃ perfect for devices like solar panels, touchscreens, and smart windows—and it does all of this while being cost-effective.
Compared to other materials like indium tin oxide (ITO), MoO₃ is more affordable and sustainable. It’s a great option for industries looking for eco-friendly materials that perform well over time. As technology continues to advance, molybdenum oxide is set to become even more important in areas like electronics, renewable energy, and smart devices.
If you're working on a project that involves thin films—whether it’s for energy, wearable tech, or displays—
MoO₃ sputtering target might be the material you're looking for.
Contact us today for expert advice on how MoO₃ can boost the performance of your project!
LATEST NEWS
2025-05-29
2025-05-22
2025-05-09
2025-04-09
2025-04-09