Comparison of Utilization Ratio Between Planar and Rotating Sputtering Target
views, Updated: 2021-09-14
According to their shapes, the commonly used sputtering targets for large area coating are divided into planar targets and rotating sputtering targets. The widely used planar sputtering targets include copper sputtering targets, silver sputtering targets, nickel chromium sputtering targets, and graphite sputtering targets. The commonly used rotating sputtering targets include zinc aluminum sputtering targets, zinc tin sputtering targets, silicon aluminum sputtering targets, tin sputtering targets, titanium oxide sputtering targets, and zinc aluminum oxide sputtering targets. The shape of the sputtering target directly affects the stability and film characteristics of magnetron sputtering coating and the utilization rate of the target. Therefore, the coating's quality and production efficiency can be improved by changing the shape design of the target to save costs.
Utilization ratio of planar sputtering target
In the magnetron sputtering process, due to the different intensity of the magnetic field distribution (the magnetic field in the tangent direction is the strongest), there is a ring-shaped "runway" (as shown in Figure 1) in the surface area of the target during the sputtering process. The utilization rate of the target is low (only about 35%).
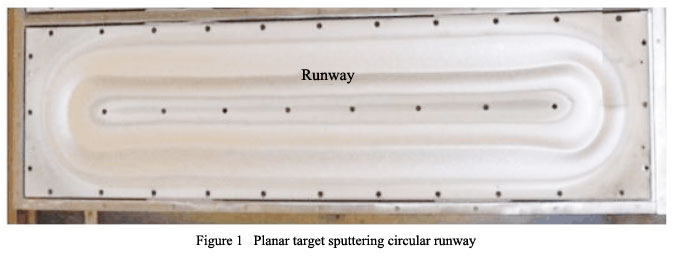
When the planar target is used, the runway's material thickness can be increased according to the actual magnetic field distribution to improve the target utilization rate and production efficiency. However, it is not easy to form a large-scale planar target, so it is necessary to prepare a small-scale target for splicing. The splicing gap provides space for thermal expansion of the target, but when the gap is large, it is easy to have air residues, which makes it difficult to vacuum. In the coating process, the release of residual gas affects the film's quality and uniformity, so the gap size should be considered in the target size design process; generally around 0.5mm is better. AEM Deposition provides a large-scale flat sputtering target with a large area coating. Further details are as follows:
Utilization ratio of rotating sputtering target
For the rotating target, the target rotates, and the sputtering area changes continuously during the sputtering process, so there is almost no sputtering track similar to the planar target. However, in the process of magnetron sputtering, the magnet steel's ring design inside the magnet steel makes the magnetic field have a certain edge effect, that is, the strength of the end of the target magnetic field is not consistent with that of the middle straight-line area.
Because of the high intensity of the end magnetic field and the orthogonal electromagnetic field's influence on the sputtering ions, the sputtering rate is fast, and an uneven etching phenomenon occurs. For the rotating target with a straight tube shape, when the material in the middle is thick, the sputtering at the edge is narrow, and the utilization ratio is generally low. Therefore, the rotating target is usually designed as dog bone (i.e., small diameter in the middle and large-diameter at both ends, as shown in Figure 2), to improve the utilization rate of the target (the utilization rate can reach more than 80%) and save production cost.
AEM Deposition provides rotating sputtering targets for large area coating. Further details are as follows:
The shape design of the target mainly affects the utilization rate of the sputtering target. Good size design can improve the utilization rate of the target and save cost. Therefore, organizations should choose the appropriate sputtering target materials according to their own needs.
AEM Deposition, as a professional sputtering target manufacturer, supplies all kinds of pure metal sputtering target, alloy sputtering target, and ceramic compound sputtering target. Further details are as follows:
If you are interested, you can click the relevant link and visit the product page. You can also email us at
[email protected].
LATEST NEWS
2024-05-24
2023-10-17
2023-10-17
2023-09-15
2023-09-15