Metal Injection Molding (MIM)
MIM Powder - Powders for Metal Injection Molding
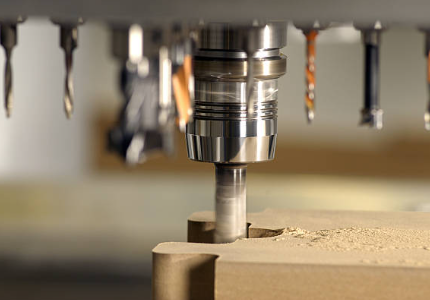
Metal injection molding (MIM) is a manufacturing process that involves injecting a feedstock made of metal powder and a binder into a mold. The feedstock is injected into the mold using a standard injection molding machine, and is then heated to a temperature where the binder burns off and the metal particles are bonded together. The resulting parts are strong and have good dimensional accuracy and surface finish.
MIM powders are the metal powders used in the Metal injection molding (MIM) process.
These powders are typically made of ferrous or non-ferrous metals, such as iron, steel, stainless steel, brass, or aluminum. The size of the MIM powders is typically in the range of 10-100 microns, and the powders are mixed with a binder to form a feedstock that can be injected into the mold.
MIM powders are used in a wide range of applications, including the production of small, complex parts with tight tolerances, such as medical implants, aerospace components, and automotive parts. They offer several advantages over other manufacturing processes, including : Low cost, high production rates, and the ability to produce parts with fine details and complex shapes.
Types of MIM Powder
There are several types of metal injection molding (MIM) powders available, depending on the specific material and properties required for the application. Here are some common types of MIM powders:
Stainless steel MIM powders:
Stainless steel is a type of metal injection molding (MIM) powder that is made of a mixture of iron, chromium, and other elements. Stainless steel is known for its high strength, good corrosion resistance, and good wear resistance, making it well-suited for use in a variety of applications. These powders are commonly used in applications that require high strength, corrosion resistance, and good wear resistance.
Nickel-based alloys MIM powders:
Nickel-based alloys are a type of metal injection molding (MIM) powder that are made of a mixture of nickel and other elements, such as iron, chromium, or molybdenum. These alloys are known for their good corrosion resistance, high strength, and good wear resistance, making them well-suited for use in a variety of applications. Such as aerospace and chemical processing applications, pollution control equipment, applications that require good electrical and thermal conductivity.
Cobalt-based alloys MIM powders:
Cobalt-based alloys are a type of metal injection molding (MIM) powder that are made of a mixture of cobalt and other elements, such as chromium, tungsten, or molybdenum. These alloys are known for their high strength, good wear resistance, and good corrosion resistance, making them well-suited for use in a variety of applications. Such as medical implants and aerospace components, valve components and bearings, cutting tools and dies.
We provide metal injection molding powder according to your customized requirements.
Characteristics of MIM Powder
Metal injection molding (MIM) powders have a number of characteristics that make them suitable for use in a variety of applications. Here are some key characteristics of MIM powders:
Particle size:
MIM powders have a relatively small particle size, typically in the range of 10-100 microns. This small size allows the powders to be injected into a mold using standard injection molding equipment and produces parts with good surface finish and dimensional accuracy.
Binder content:
MIM powders are typically mixed with a binder to form a feedstock that can be injected into a mold. The binder content of MIM powders is typically in the range of 15-30%, and the type of binder used can affect the properties of the resulting parts.
Density:
The density of MIM powders is typically in the range of 7-9 g/cm3. This density allows the powders to be injected into a mold using standard injection molding equipment.
Compressibility:
MIM powders should have good compressibility in order to be easily molded into complex shapes. This is important for producing parts with fine details and complex shapes.
Strength:
MIM powders should have good strength in order to produce parts that are strong and durable. The strength of MIM powders depends on the type of metal used and the specific alloy formulation.
Chemical Composition
Alloy | Norminal Composition (wt%) | |||||||
---|---|---|---|---|---|---|---|---|
Cr | Ni | Mo | Cu | C | Si | Mn | Fe | |
304 | 18-20 | 8-12 | - | - | ≤0.08 | ≤1 | ≤2 | Bal |
316L | 16-18 | 10-14 | 2-3 | - | ≤0.03 | ≤1 | ≤2 | Bal |
17-4PH | 15.5-1735 | 3-5 | Nb:0.15-0.45 | 3-5 | ≤0.07 | ≤1 | ≤1 | Bal |
420 | 12-14 | - | - | - | ≤0.25 | ≤1 | ≤1 | Bal |
430 | 16-18 | - | - | - | ≤0.12 | ≤0.75 | ≤1 | Bal |
440CN | 16-18 | ≤0.6 | ≤0.75Nb:1.5-2.5 | ≤0.5 | 0.9-1.25 | ≤1 | ≤1 | Bal |
Physical Properties
Particle Size |
Tapping Density(g/cm³) |
ParticleSize Distribution (um) |
||
---|---|---|---|---|
D10 |
D50 |
D90 |
||
-400F |
4.8-5.1 |
4.5-5.5 |
14.5-15.5 |
25-32 |
-500F |
4.6-5.0 |
4.3-5.2 |
12.5-13.5 |
22-27 |
D90:22 |
4.6-5.0 |
4.0-5.0 |
11.5-12.5 |
19-23 |
Note: Other specifications are available upon any customer requirements.
MIM Powder Manufacturer
AEM Deposition is a China manufacturer of MIM (metal injection molding) powders. Our company has a long history of producing high-quality MIM powders for a wide range of industries, including medical, aerospace, and automotive.
We are committed to providing our customers with the highest level of service and support, and we strive to continuously improve our processes and technologies to meet the evolving needs of the market.
Our MIM powders are made using a unique process that combines the precision of injection molding with the versatility and strength of metal. At AEM Deposition, we are dedicated to providing our customers with the highest quality MIM powders and the best possible service.
If you are in need of MIM powders, we encourage you to contact us to learn more about our products and how we can help you succeed.
Service every customer with care & professional.
Integrated Production Line
AEM is equipped with a complete set of production and processing facilities in particular high standard cleaning room .
Strict Quality Control - ISO9001
AEM runs a strict quality control system involving raw materials selection, production control, product inspection, fine packing.
Comprehensive Solutions - Timely service
we can help customers select materials, design products, and provide full technical and after-sales service support.
Applications of MIM Powders
MIM (metal injection molding) powders are used in a wide range of applications across many different industries. Some common examples include:
Medical devices:
MIM powders are commonly used in the production of medical devices, such as implantable joints and bone screws. They are highly biocompatible, making them ideal for use in medical applications.
Aerospace:
MIM powders are used in the production of aircraft components, such as bearings, gears, and structural parts. They are known for their strength and durability, making them ideal for use in high-stress environments.
Automotive:
MIM powders are used in the production of automotive parts, such as valve springs, gears, and steering components. They offer a high strength-to-weight ratio, making them ideal for use in the automotive industry.
Consumer products:
MIM powders are used in the production of a wide range of consumer products, including appliances, sporting goods, and electronics. They offer a high level of precision and detail, making them ideal for use in consumer products.
Industrial equipment:
MIM powders are used in the production of industrial equipment, such as pumps, valves, and gears. They offer a high level of strength and durability, making them ideal for use in industrial applications.